On the cutting edge of the Fourth Industrial Revolution
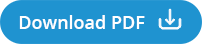
In a nutshell
Digital transformation is as essential and inevitable in industry as it is in any other area of business. The opportunities offered by the likes of the Industrial Internet of Things (IIoT), digitalization and ubiquitous connectivity are just too great to ignore, as are the risks of inactivity.
In this context, we can say that pervasive digitalization is taking us into a fourth industrial age, often referred to as Industry 4.0. These terms might seem grandiose, yet they reflect a paradigm shift in how industry operates. Digital transformation is helping companies become more flexible, responsive and aware, as well as more innovative, productive and efficient. This is true whether it is in the office, the factory, the warehouse, the logistics chain, in healthcare or elsewhere.
There are challenges involved though, one of the biggest being how to process the huge amounts of disparate data involved. In this paper we look at why this is driving industry to do more – including the application of AI technologies – at the network edge, and at how this can be efficiently achieved.
From hardware-first to software-defined
What’s different with Industry 4.0 is that previous industrial revolutions were essentially about building and employing better and more efficient hardware. The introduction of water, steam or electrical power, the invention of the production line or the addition of computers and programmable controllers – all these things aimed to improve the physical technology and processes used within factories, hospitals, warehouses and other ‘silos of activity’.
Industry 4.0 is instead built upon software, and on automation and communication. It is about getting more information from the hardware, and then communicating and analyzing that beyond the siloed local processes, with fast feedback to the hardware if need be. And just as digital transformation is changing the office, Industry 4.0’s ‘cyber-physical’ systems have the potential to disrupt and change how manufacturing and other areas of industry function.
The challenge for the CIO and COO is that this means your operational technology is no longer discrete. For example, the smart factories of Industry 4.0 are connected factories – their smart machinery is on the industrial Internet of Things, and they must communicate with the rest of your organization and its supply chain – and potentially with the world beyond. The same goes for your vehicle fleet, the medical devices around your hospital, your inventory management systems, and much more.
All this distributed yet intrinsically-connected technology gives your IT network yet another edge: after the office edge and the mobile edge comes the industrial edge.
Digital industrial transformation
Just as today’s office network edge connects users and their devices with the core enterprise network and then the Internet, the industrial edge too is a connection medium – a bridge between your operational technology and your enterprise IT systems. On one side, you have operational technology that needs to send and receive messages. On the other, you have enterprise applications such as SAP, Oracle and so on, and of course these applications may be hosted locally or in a cloud.
There are several challenges here. One of the biggest is that there are so many different things on each side. On the operational side there are sensors, actuators, meters, programmable logic controllers (PLCs) and so on, all of them generating (and consuming) data. On the IT side there are many different applications that could use that operational data. Bridging this level of many-to-many complexity is not trivial, as it means translating multiple data flows simultaneously.
To make it even more complicated, few companies have only one supplier of industrial equipment, and some of that equipment, especially in manufacturing, may be 20 years old, or older. So there are many communication protocols that must be catered for, and that’s even before we start thinking about adding new IIoT-style sensors to existing equipment that was not designed for digital operations.
In short, Industry 4.0 moves us from siloed factory-wide (or site-wide) systems to systems that connect not just to the enterprise but to its wider value chains. The software this requires is very different from most of today’s process control or manufacturing systems, being both more sophisticated and more connected.
Another major challenge is the sheer volume of data that the operational technology can generate. We could well be talking about hundreds or thousands of sensors and other devices, and different kinds of data too. Some data is temporal – a status signal that only matters when it changes, say – while other data has longer term value, for example it could be analyzed to help plan preventative maintenance.
Sending all this data to the core would be impractical both in terms of available bandwidth and processing capability. Moving the first stage of processing and analytics closer to the edge helps fix this, by reducing the data volume that would otherwise be sent to the enterprise systems for deeper analysis.
The edge computing platform
Fortunately, this need for many-to-many translation and connectivity is something that a suitable platform (appliance/gateway) can be designed to handle. The flow logic is largely consistent, even if the applications, message formats and transport protocols are very different. What’s needed is an intelligent device which can run analytical software to handle the messaging flows and conversions in real-time (Figure 1).
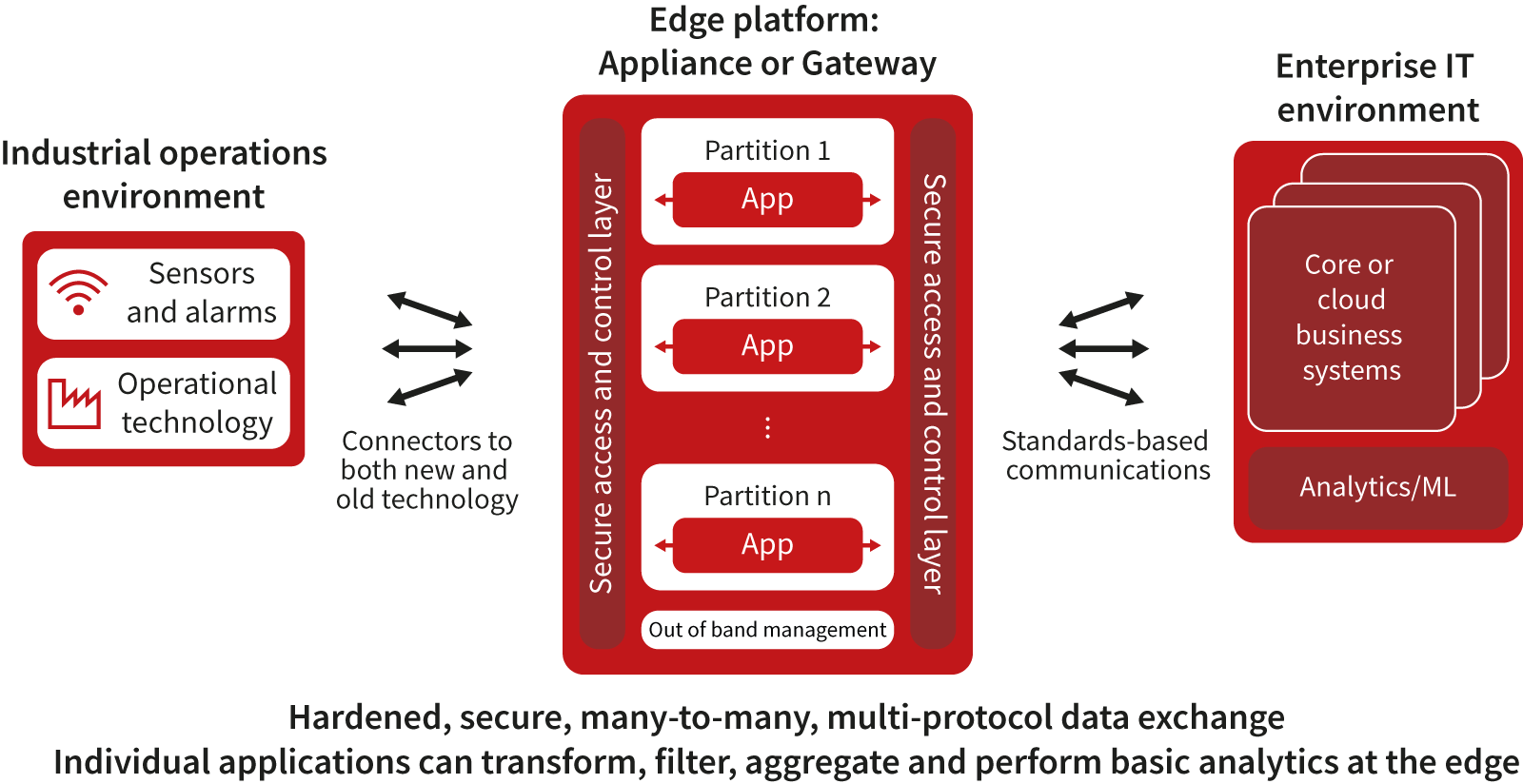
Figure 1 – Enabling Industry 4.0
Of course, all this data and the business and operational systems that generate it can be highly sensitive and mission-critical. That means the edge platform needs secure access and control, plus sandboxing or partitioning for its applications, and the more general ability to isolate data flows.
At the same time, such an edge platform ought to be open and standards-based, and use hardened and resilient industrial-grade hardware and software. In addition, it should be possible to daisy-chain these boxes together for scale. For resilience they need to be able to operate offline as well, because industrial equipment at remote or mobile locations may not have reliable or fast network connectivity.
The edge platform should also feature encrypted communications and timely updates and software patches, with software that is digitally-signed for authentication and verification. Automated and centralized management are essential, of course.
Perhaps less obviously, the edge platform also forms a bridge between IT and operations, so it needs to be compatible across departmental purchasing boundaries. That is because it is common for IT and operations to have separate budgets and different buying criteria and practices.
The fog of data
A potential risk of industry 4.0 is that the huge amount of data generated at the edge can make it difficult to work out exactly what is really happening. Not only can this “fog of data” make it hard to see what’s going on, it has the potential to overload our business systems and/or jeopardize the connections to them.
Filtering this data for useful information is an ideal application for machine learning (ML), the AI-derived technology which trains algorithms to recognize patterns in data and draw conclusions from them, much as a human would, but far faster and taking in far larger volumes of data.
Traditionally one would think of applying ML using powerful computers in the core or perhaps in a cloud, but if we can do at least some of this filtering at the edge (for example, by deriving rules in the core and pushing them out to the edge), then we can also address the data reduction challenge.
Deep analysis of the reduced data will still require high-performance computing in the cloud or data centre. And of course, making the right decisions requires the right algorithms, which for most organizations will mean finding a technology partner with expertise in this area and access to these kinds of resources.
The bottom line
Industry 4.0 and the fourth industrial revolution are defined by software. Digital industrial transformation, just like digital transformation in the office, has the potential to enable new workflows and smoother collaboration. In the process, it can introduce whole new ways of working, whether that’s in the factory, in logistics, in healthcare or in the field.
However, while there might be fewer people-related issues in Industry 4.0, the technology required at the industrial edge can be much more complex compared to its office-based equivalent. Among other factors, that’s due to the variety and cost of the hardware and software involved, and the large volume of data that IIoT connectivity can generate. In addition, most industrial systems do not have a heritage of being network-connected, so it’s likely that there will also be complex protocol conversions and security considerations to take into account.
There is no ‘one size fits all’ solution for Industry 4.0. However, if organizations are to avoid the expense and complexity of implementing multiple overlapping individual solutions at the industrial edge, there is a more efficient route. That is to build – if you have a strong background in both industrial automation and the business IT systems that Industry 4.0 connects to – or acquire a suitable multi-protocol appliance.
Bryan Betts is sadly no longer with us. He worked as an analyst at Freeform Dynamics between July 2016 and February 2024, when he tragically passed away following an unexpected illness. We are proud to continue to host Bryan’s work as a tribute to his great contribution to the IT industry.
Have You Read This?
Generative AI Checkpoint
From Barcode Scanning to Smart Data Capture
Beyond the Barcode: Smart Data Capture
The Evolving Role of Converged Infrastructure in Modern IT
Evaluating the Potential of Hyper-Converged Storage
Kubernetes as an enterprise multi-cloud enabler
A CX perspective on the Contact Centre
Automation of SAP Master Data Management